My journey in woodfired ceramics has spanned over 55 years. I fell in love with woodfiring whilst still a student at the University of New South Wales (UNSW). I knew little about the process, but by the end of seven years as an undergraduate making pots and conducting research on woodfired celadon glazes, I developed a fascination for the process. This exploration continued through six successive kilns with Bourry-style fireboxes, all in different locations and with their own individual firing characteristics that provided a continuous learning process along the way through changing ceramic works.
I learned to love the interaction between the pots, the fire, and the potter. The constant attention to the fire over a long period of time was at times a meditative process, at other times exhausting, wondering when the final temperature would be achieved. I have written a number of times about cycles in life, especially for those who pursue woodfiring where quite often, the making, packing and firing of large kilns creates a substantial routine repeated over and over again. In my case, I started out firing a small kiln, and passed through ever larger ones until the ageing process required me to downsize my kiln back to about the size of the first kiln I worked with, representing a cycle that would soon come to an end.
“I learned to love the interaction between the pots, the fire, and the potter»
Kiln one had 12 cubic feet of setting space in one chamber, built by Terry Golvin at UNSW circa 1973.1 This kiln was used for my research on firing conditions and celadon glazes.2 I learnt to be patient and let the kiln do its job, resisting the entreaties of various people to do things on a whim. Reduced cooling of the kiln happened a couple of times when wood was not cleared off the hobs after reaching temperature before sealing up the kiln. The image of the casserole is from one of these reduction-cooled firings.
Kiln two had 30 cubic feet of setting space in two chambers, designed and built by Ivan McMeekin in Woronora, on the southern outskirts of Sydney, New South Wales. In 1975, Ivan allowed me to use his workshop at Woronora for the 12 months he was in the Tiwi Islands after Terry Golvin died. The clay body was made by hand using Woronora red clay and Cresta BB clay as the base, with feldspar and quartz additions (the same recipe was used at UNSW). The pots were raw-fired and sold at various places around Sydney, including the Potters’ Society gallery and Libby
Gordon’s gallery in Artarmon. The first firing of the kiln was excellent, and the second firing disappointing. It provided an introduction to the vagaries of woodfiring, especially when firing a kiln with which I had little experience, despite my repeated experience working with the singlechambered kiln at UNSW.
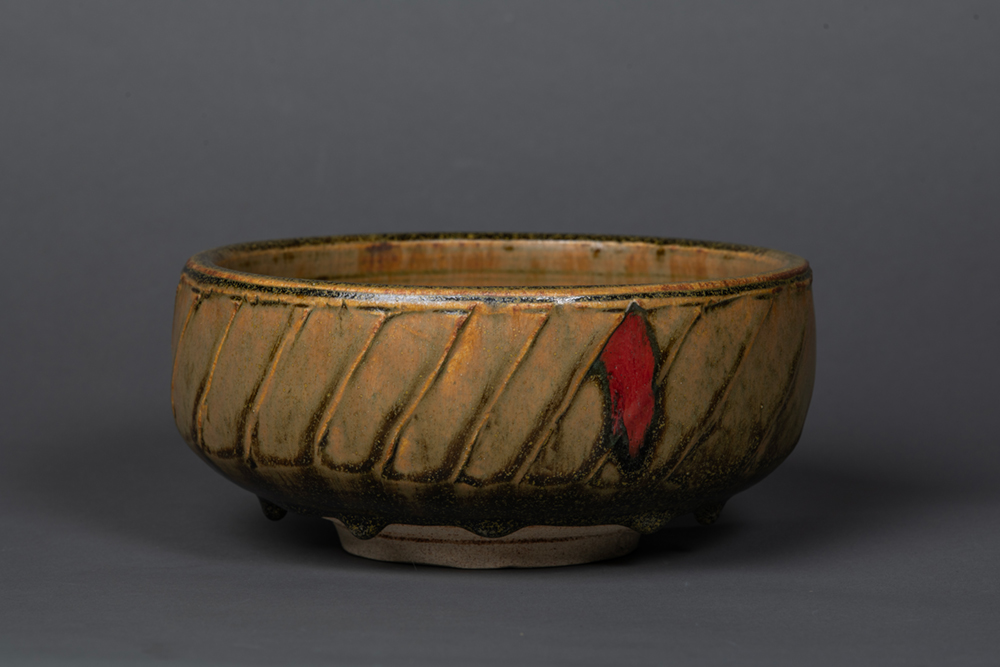
Kiln three had 40 cubic feet of setting space in two chambers, built by Tiwi potters Eddie Puruntatameri, John Bosco Tipiloura, Terry Golvin, Ivan McMeekin, and Alf Caldwell (the UNSW technician) in 1973–74. The kiln was located in Wurrumiyanga (formerly Nguiu, Bathurst Island, Northern Territory), and used some firebricks around the firebox and bagwall, insulation bricks for lining, and had outside walls built from locally-made house bricks. I worked with Tiwi Potters Eddie Puruntatameri, John Bosco and John Patrick Kelantumama there; it was an immersive cultural experience as it was very isolated, and just after Cyclone Tracy had devastated Darwin. The pottery sourced and processed local materials to make raw-fired stoneware. The clay sources were Parapoli swamp clay and Tudiangini white clay used for ceremonial purposes, fluxed with granite from Rum Jungle south of Darwin.
It was my first experience of woodfiring in the tropics – the 100% humidity and about 34°C during the wet season were exhausting firing conditions, which prompted a change in the firing routine to have maximum temperature in the late evening instead of the middle of the day. It was also the first time I experienced reduction in chamber one and mainly oxidation in chamber two, from allowing the kiln to progress during firing just as it wanted to. The oxidation glazes were based on PhD research carried out by Barry Heatherington on oxidised stoneware. I made only a few pots there, as the main aim was for locals to make pots to fill the kiln. Pictured is one of the few pieces I made, collected by Johanna Winchcomb in 1977 and returned to me in 2024.
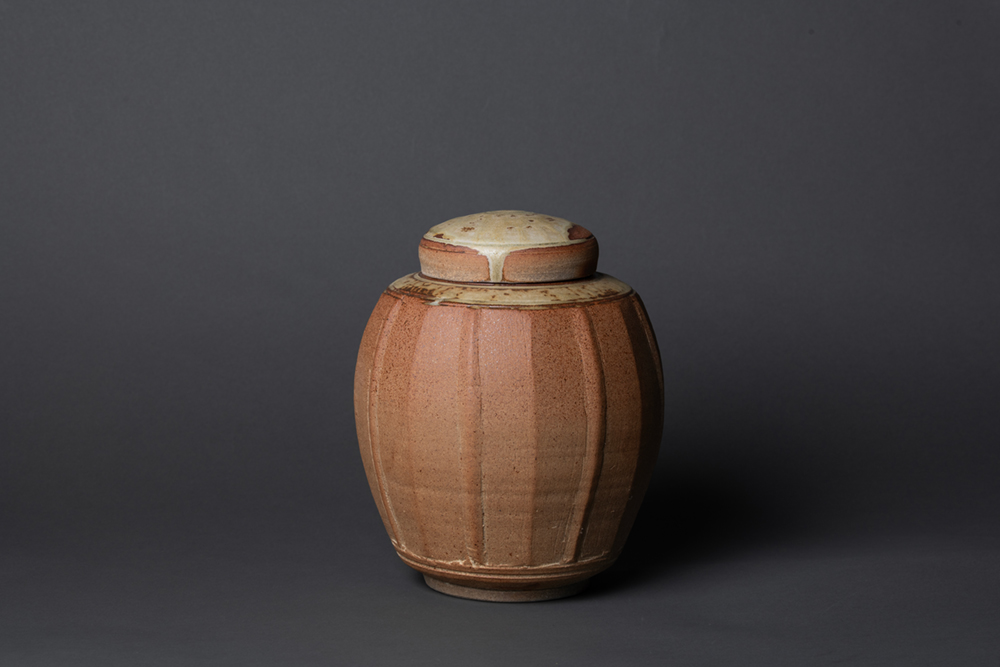
Kiln four had 90 cubic feet of setting space in two chambers. This kiln was built on my property at Whiteman Creek (Bundjalung Country) in 1979–80, and was based on the Woronora and Bathurst Island kiln designs, but much bigger. Some changes were made to the design, such as introducing preheated air channels for chamber two. This was not very successful as the channels became blocked as they passed under the ash pit floor and up behind the bag wall and under the floor in chamber one. The secondary air inlet in the firebox was enlarged to ensure sufficient air for the side-stoking of chamber two.
Originally all the shelves were made by hand utilising Pugoon 156 clay mixed with two grades of alumina grog. These shelves were fired in the first firing of the kiln before any pots were made. The wood used to fire the kiln was from red gum and spotted gum trees that had been ringbarked to create grazing paddocks for cattle. Using this wood required felling trees, cutting blocks to length with a chainsaw, then splitting them down. It took about two days of splitting to produce enough wood to fire the kiln and split the smaller sizes to side-stoke chamber two.
The pots were raw-glazed and reduction-fired in both chambers. I drew on my research on local materials from my Master of Science in 1980.3 I had no pugmill, so the day started with wedging 60-odd pounds of clay, then throwing on a kick wheel in the morning, turning, handling, and glazing in the afternoons. I made mainly domestic stoneware with a few porcelain experiments. White glaze breaking to brown was used, with a brushwork fish motif decoration using iron pigment. Glazes included green chun, tenmoku, and celadon glazes. I started testing a porcelain body using Elsmore kaolin that was translucent and interacted with the poplar tree ash I collected locally. This became the basis for the porcelain I made until 2024. The making was a six-week cycle – four weeks making pots, one week packing and firing, unpacking, and clean-up, and one week taking pots up and down the north coast of New South Wales to various galleries.
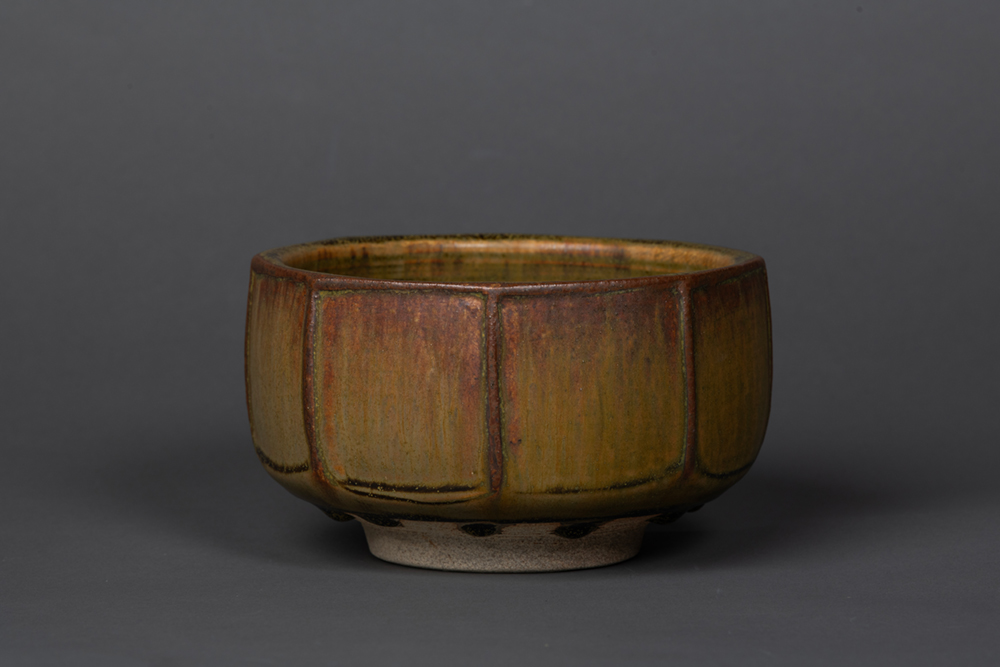
Kiln five had 140 cubic feet of setting space with a Bourry firebox and two chambers, built in 2002 over about six months with the help of Kerry Selwood and others. The design was adjusted
for bigger pots, with four stacks of 16×20 inch shelves in each chamber. Bigger shelves were then purchased, 24×24 inches, which could be accommodated within the setting. The preheated air
design was changed, passing under the floor of chamber one from the side of the kiln and into the throat of chamber two.
The kiln was also designed to accommodate the maturing potter’s decreasing flexibility by increasing the doors to two and a half bricks wide.4 This kiln was fired for over 20 years. Originally I fired mainly stoneware with some porcelain, but this developed into nearly all porcelain. Pieces were thrown, slab-built, and slipcast. Big porcelain pots were thrown in three
sections and joined together, and nearly all work was now bisque-fired as the porcelain could not cope with thickly applied raw glazes. Slipcasting was introduced for porcelain forms that could not be thrown, with models and moulds made on-site to suit various shapes and sizes. Pots were often cast and then carved, some pieces were cast and then thrown, or added to with slab-built sections.
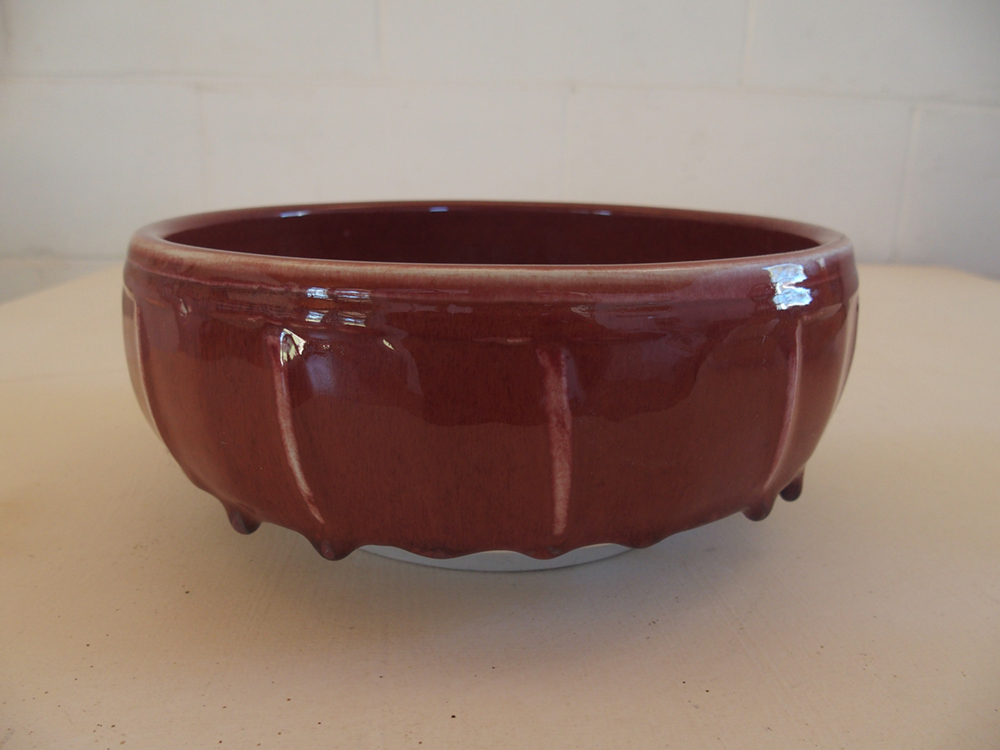
Kiln six was a single-chamber Bourry firebox kiln with about 16 cubic feet of setting space, built in 2022 with help from Kerry Selwood and Steve Sawkins. It was designed around shelving from the large, retired kiln (kiln five), with two stacks of 16 × 20 inch shelves side by side in the chamber. This is so an ageing potter could still keep working.5 Utilising local raw materials for both clay bodies and glazes, I returned to making stoneware, and Golden teadust (developed from a local rock), celadon, chun and ash glazes. A copper red glaze that I used for many years in the big woodfired kiln (kiln five) was fired with no special conditions on open kiln shelves. It worked best in the second chamber, where the temperature rose very quickly up to about 1320°C and cooled quickly at the end of the firing. This copper red glaze on porcelain amazingly still worked in kiln six. Large examples have been acquired by the Powerhouse Museum (from kiln five) and Shepperton Art Museum (from kiln six). Kiln six has been fired 11 times over the past four years. The last firing was in August 2024.
The cycle I mentioned earlier is a return to a kiln similar in size to that first kiln I fired at UNSW some 55 years ago. It marks an endpoint to the journey of woodfiring and exploring local raw materials, as my body will no longer allow me to pursue the physical requirements needed. I don’t have an interest in electric kilns and using all-bought ceramic supplies, so the cycle has ended, and what I have achieved will remain as it stands.
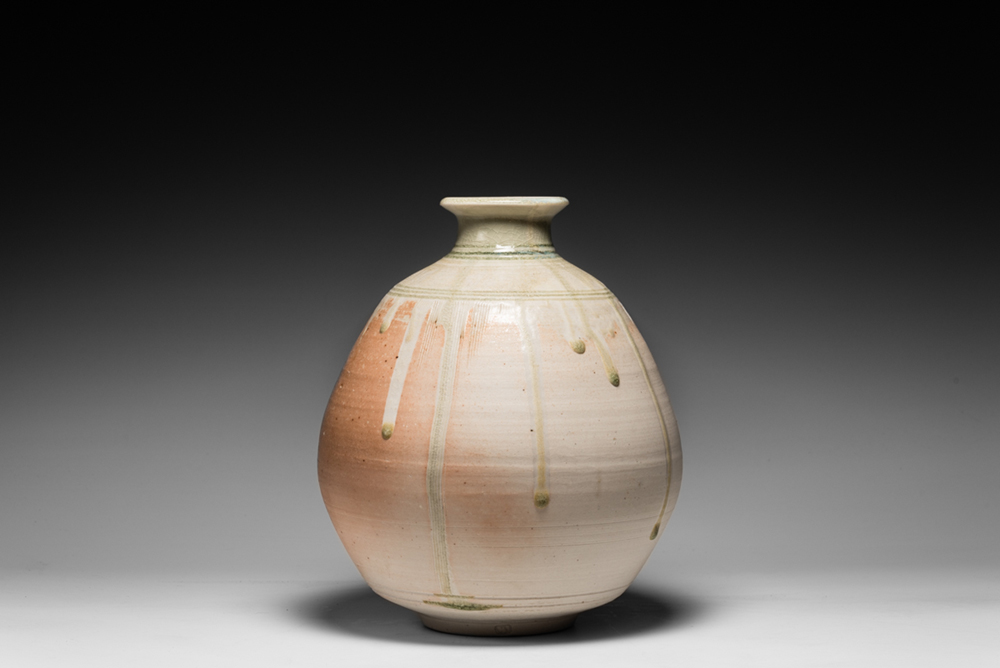
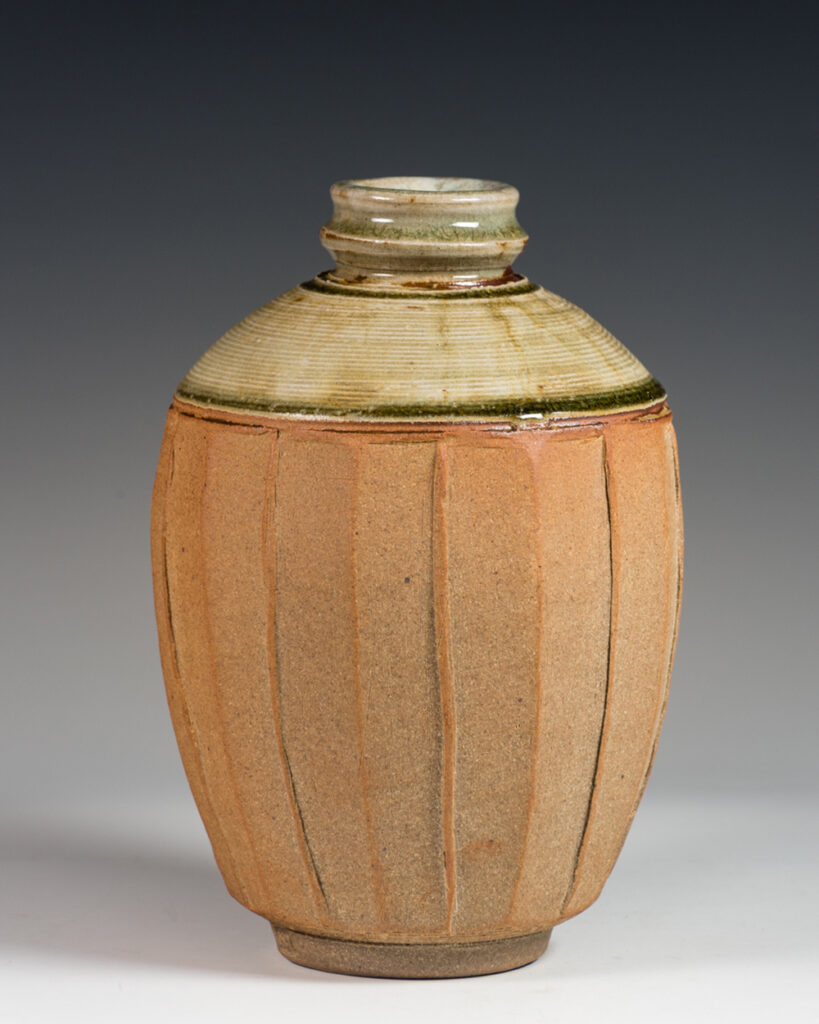
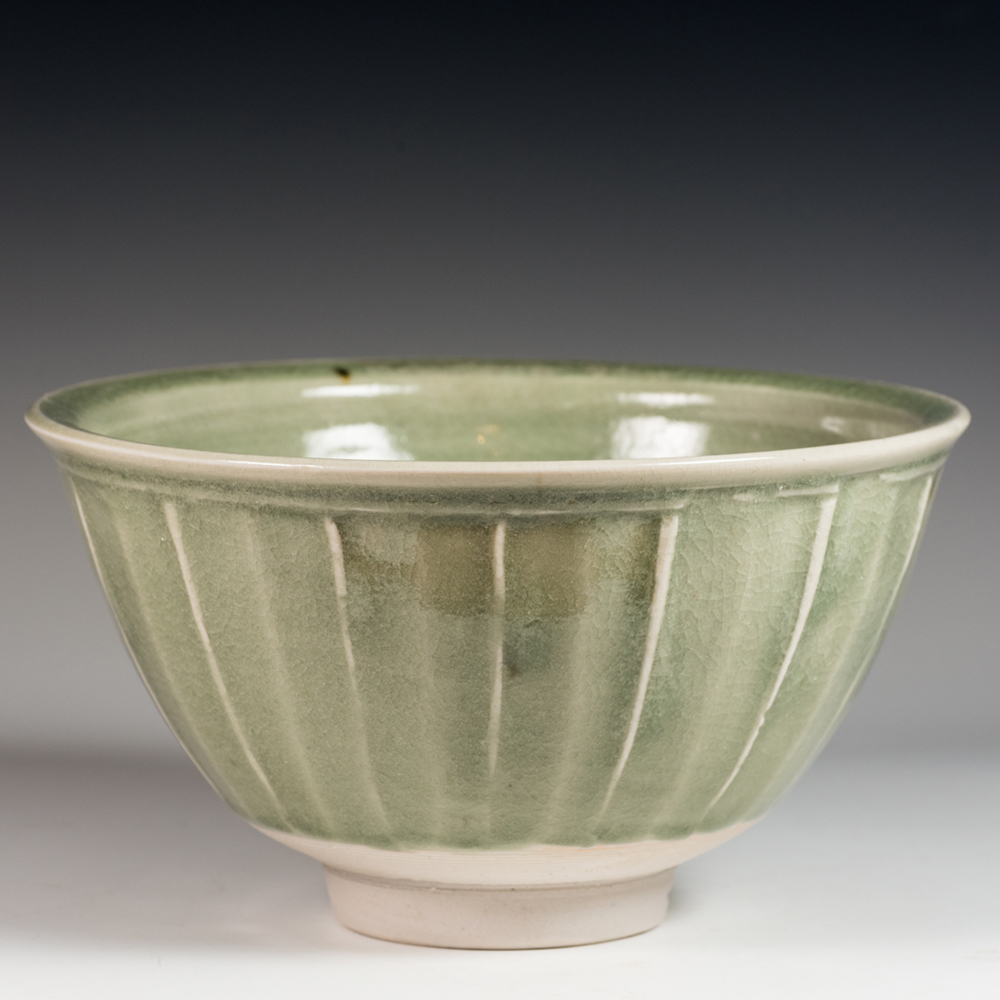

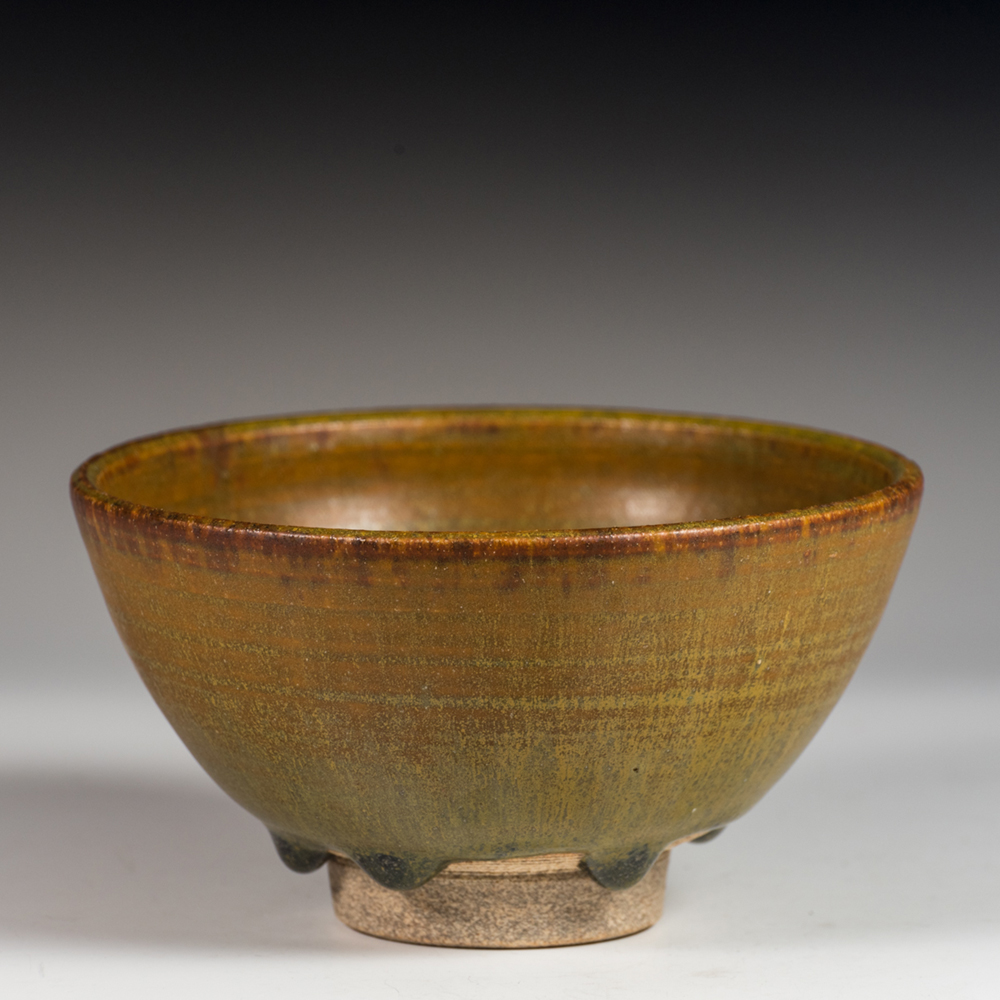
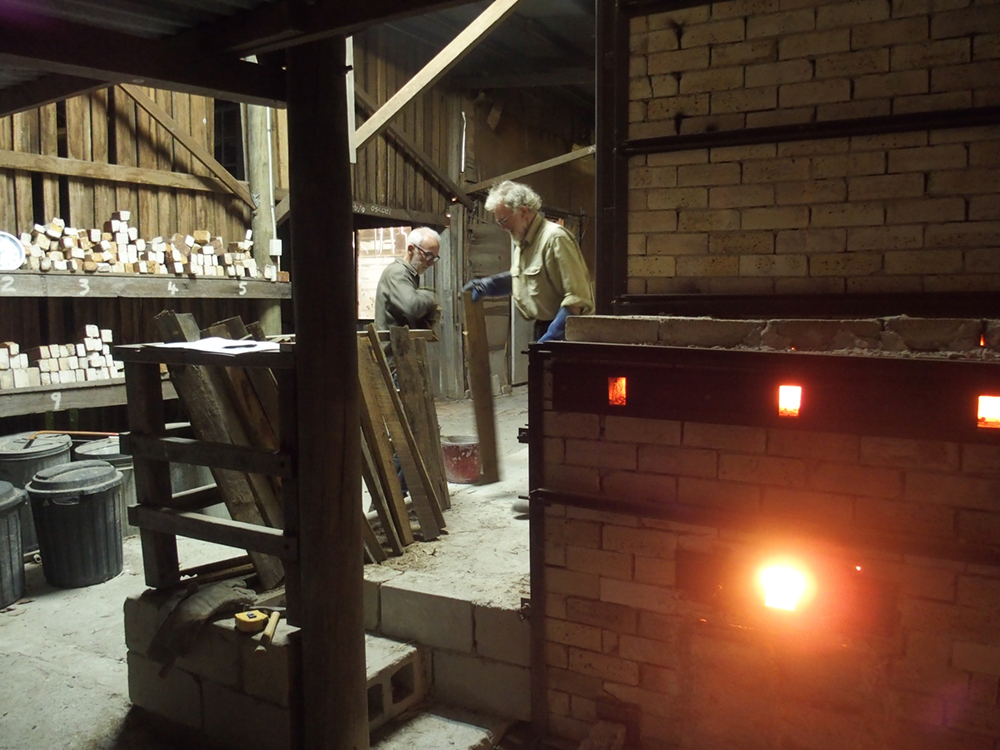
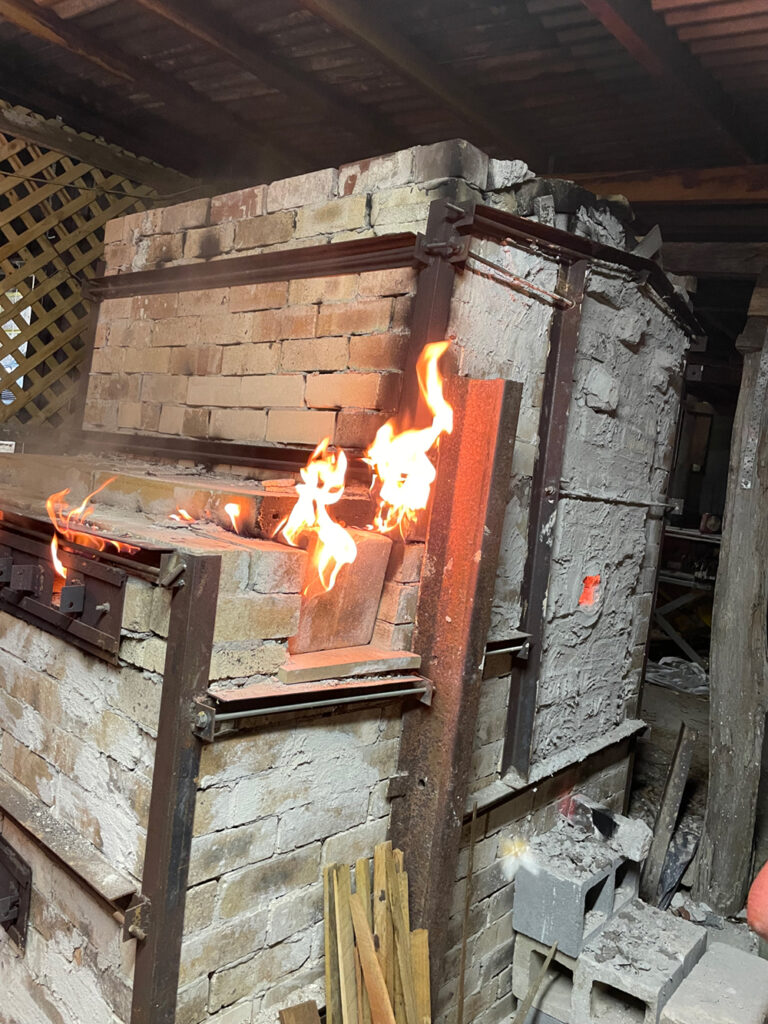