Working with clay is a way of life. John Hunter has been potting for 54 years and now resides in Pennsylvania after living in Windhoek, Namibia from 1997 until just last August. He leads Community Hope School with his wife, Suzanne. While some of the funds for their program come from local and international donors, Hunter’s pottery is still a source of income for the Lighthouse, their new after-school center.
The Hunter’s worked in Windhoek for 2 years training teachers and in 2005 established a primary school in the township of Katutura where the majority of blacks live since their forced removal from the centre of Windhoek in 1959. Community Hope School grew and became very successful until in 2020, when because of Covid-19 they decided to turn it into a more sustainable after school program for their learners. “Empty Bowl” events at exhibitions of John’s pottery have been useful to promote Community Hope and share the need for quality education. Rather than relying on local potters to donate bowls for events, Hunter has produced over 5000 bowls at his studio with a Bailey Clay Extruder donated by Jim Bailey in the USA. This unique way of forming bowls without a wheel has been a way to train his local apprentices in production pottery giving them skills needed to be successful potters themselves.
Hunter has been working with clay since 1968. 2018 marked 50 Years of John working with clay. After spending the summer of 1960 at Arrownont School of Arts and Crafts and then in 1970 Penland School of Crafts with Cynthia Bringle and other well know potters and ceramic artists such as Toshiko Takaezu, Bruno LaVerdiere, Jane Peiser and others he launched his career at “The Pot Shop” in Venice Beach, California where he met master potter, Ned Sloane. Bringle’s, Takaezu’s and Sloane’s influence of Asian ceramic style stuck and he developed a love for the simple yet elegant work of Shoji Hamada and Bernard Leach that has guided his work until the present day.
While Hunter’s true passion is education and teacher training, working with clay is central to all he does. He doesn’t hold pottery classes as such but has done workshops worldwide with his potter’s wheel, demonstrating throwing, glaze decoration and Sumi-e brushwork for potters in Southern Africa, Europe, Australia, the Middle East, and North and South America.
He worked out of his Namibian studio, The Potter’s House, 20k North of Windhoek in Brakwater until last August. He uses electric, gas and wood-fired kilns to finish his work. In 2017 at the Potter’s Association of Namibia’s Biennale two of his Elephant Mug Sculptures were awarded the Premiere Award and purchased by the Namibian Arts Association for their permanent collection. In 2019 he again won the Premiere Award for a wood Fired Tea Pot.
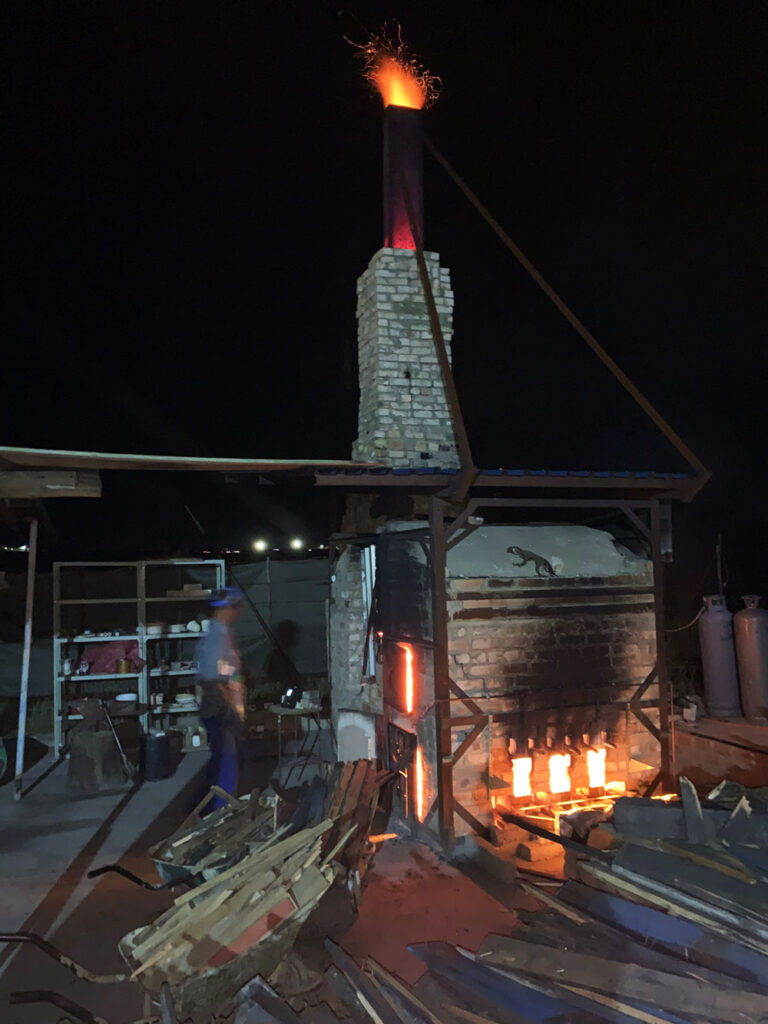
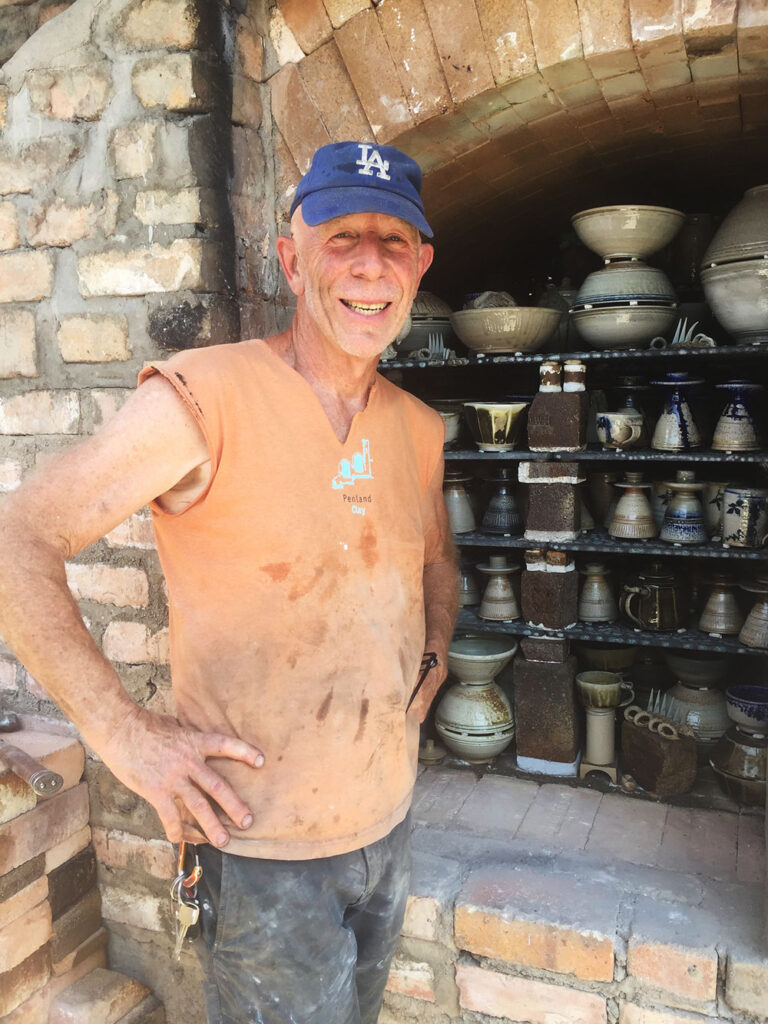
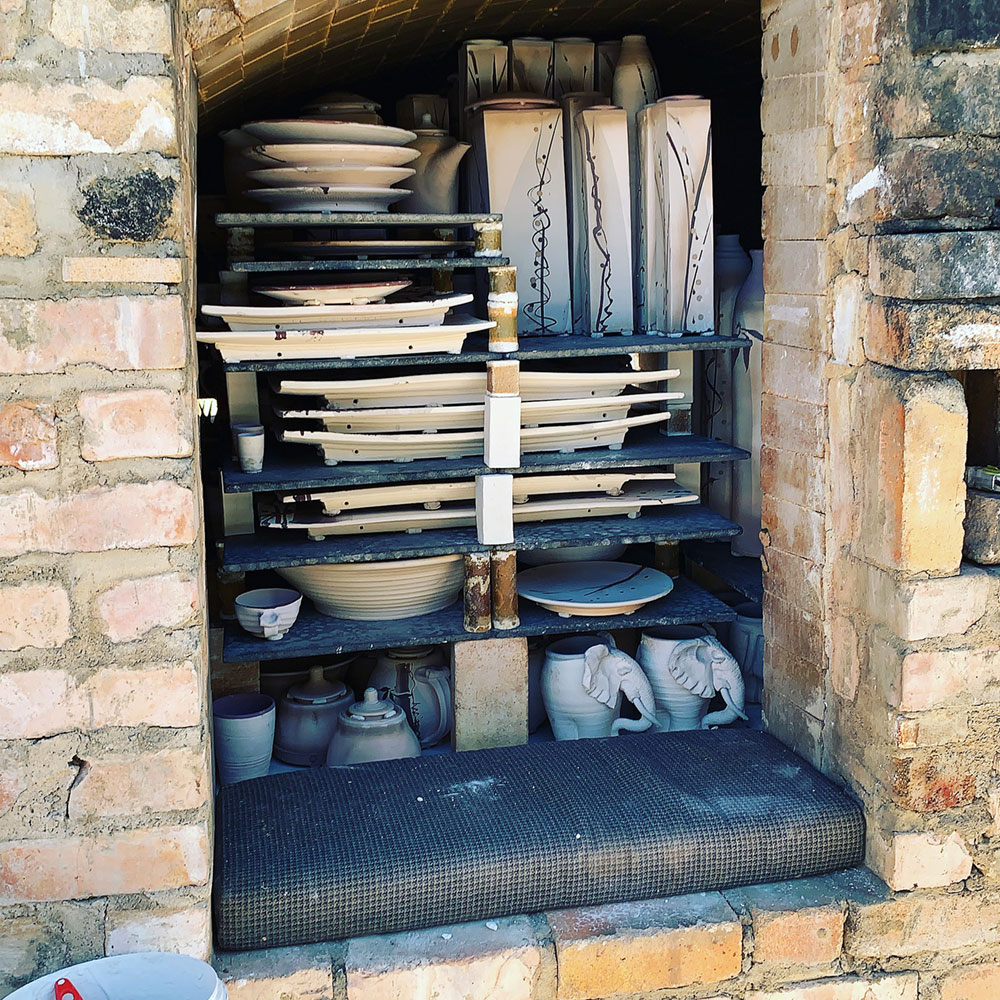
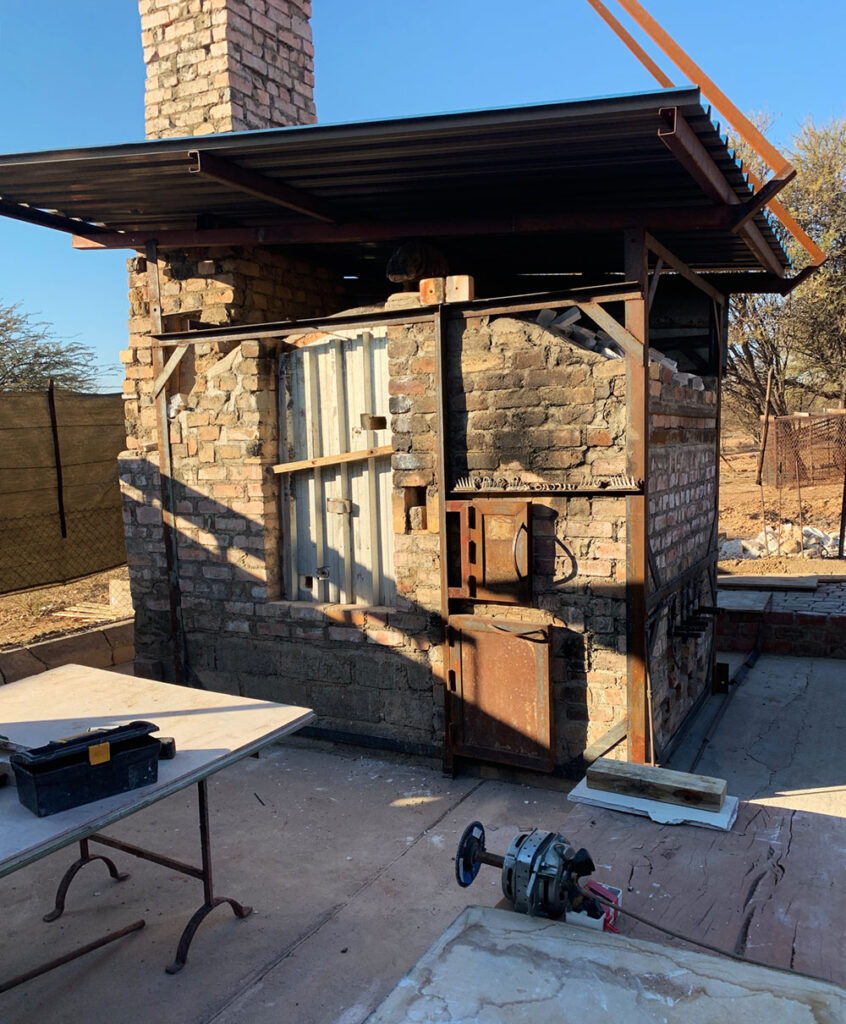
After moving to a new studio and home last year Hunter built a 50 cu. ft. wood fired, cross-draft, salt glaze kiln from 10 tons of magnesia bricks donated by Ohorongo Cement. This was a construction challenge as it was not only 3 times the size of his former Phoenix Fast Fire wood-fired kiln, all the bricks were perfectly square 198mm x 198mm but tapered to make a 3 or 6 m circle. These, along with bricks salvaged from his previous kiln made up the inner courses of firebox and chamber. The magnesia bricks were not only tapered but presented the challenge of being extremely dense and therefore heavy, weighing 8K each. The arch alone weighed 1 1/2 tons. Although the bricks were rated to 1700 ºC, they were not waterproof and would disintegrate if fired wet as the magnesia turned into Magnesia hydroxide! A nine-inch course of old fire bricks and common red bricks produced here in Namibia were used as an outer course over a layer of off cuts of hard 1100 ºC 75mm insulation board also donated by Ohorongo Cement that was used in their commercial lime kilns.
What should have been a two-month project turned into four as it was discovered that the original steel buttressing was not sufficient to hold the weight of the arch. A re-do was necessary and stronger steel angle iron and bracing top and bottom were added as well as adding another outer course to the walls of the kiln to add mass and protect the magnesia bricks from the rain, because, when it does rain in Namibia, it can rain buckets. A steel roof was added to cover the kiln and an extra high chimney eight meters tall was built to provide adequate natural draft considering the altitude being almost 1700 m in Windhoek.
The 450mm walls of the kiln make it look larger than it really is and when fired it takes five days to cool. The arch stretches from the firebox wall to the back wall and chimney and has a span of 1800mm (6ft). The height is 1200mm (4ft) and depth is 1120mm (44in.)
The design was modified from an article in December 1977 issue of Ceramics Monthly, Two Wood Fired Kilns. Hunter had built the other kiln, an 8 cu. ft. cast-able kiln, Smaug, (named after the dragon in J.R.R. Tolkien’s “The Hobbit”), at Cabrillo College in Santa Cruz, California in 1978 with his son, Christian, who was five at the time. He was Professor of Internal Medicine and Physiology in Namibia at UNAM’s College of Health Sciences until he moved back to the US in 2021. He helped Hunter build the new kiln as well.
Olsen’s “The Kiln Book” also provided the plans for a cross draft salt kiln he built in Japan and then again in the US. Combining the better of the two designs was how the final plans of the kiln we achieved.
Firing a bespoke kiln for the first time is always a challenge and learning experience. After loading pots for two days, wadding and stacking each piece carefully to allow enough draft of the fire and fumes through the ware, the door was bricked up and thermocouples and cone pads placed in strategic places. Candling the kiln overnight with first two Ward gas burners and then adding a channel iron drip waste oil burner gets the kiln to 300 ºC by first light when wood firing commences. The long day of stoking went on to midnight when salting began at cone 12. Results were varied as would be expected and plans are being made to add more folks to the team and stoke for at least 24 hours to even out the temperatures and increase the ash build-up. The magnesia bricks showed almost no salt build-up and this will allow the kiln to be used for wood alone as well as the salt glaze in separate firings.
Hunter plans to publish a guide to Kiln Building for the Complete Idiot soon, with detailed instructions of what not to do!
While Hunter’s love of clay and fire provide a baseline for his life and work it is his passion for education that truly inspires him. The opportunity to bring the quality of learning that his own children had into the Damara location at Community Hope is what drove him. Selling pots in Namibia with its limited population and lack of sophistication for ceramic art as a whole has been a challenge and Hunter packed up most of his pottery for sales in the USA and Europe each year as he and his wife traveled and fundraised for the school. He continues to lecture at churches and schools to find sponsors for the Community Hope Lighthouse.
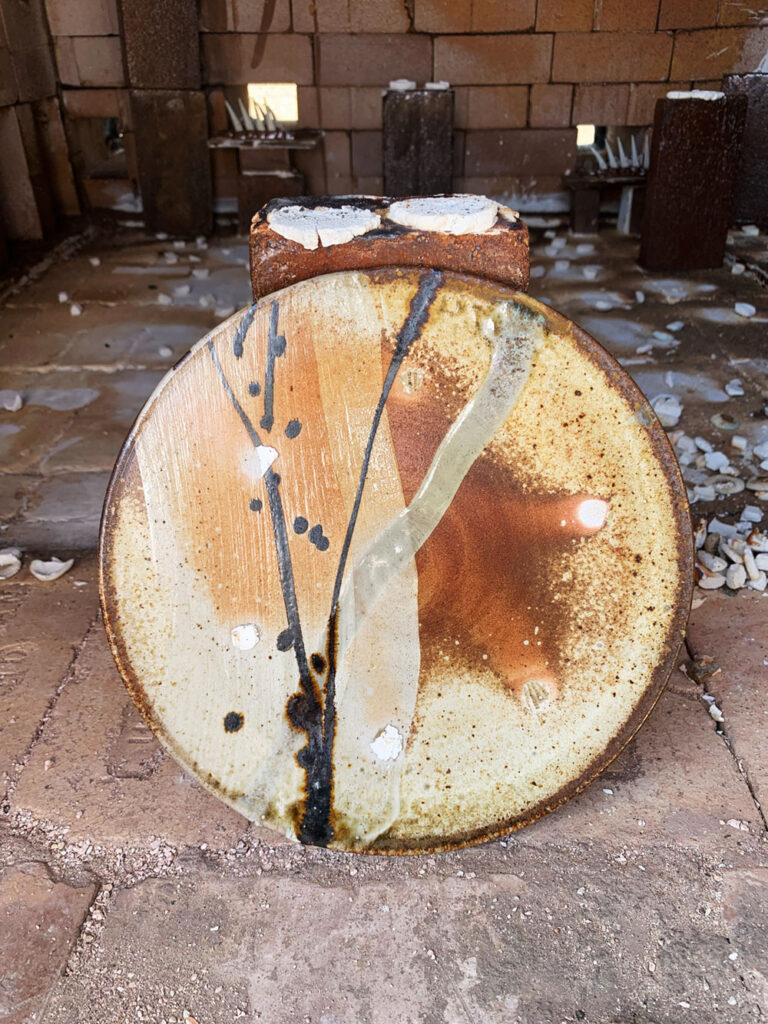
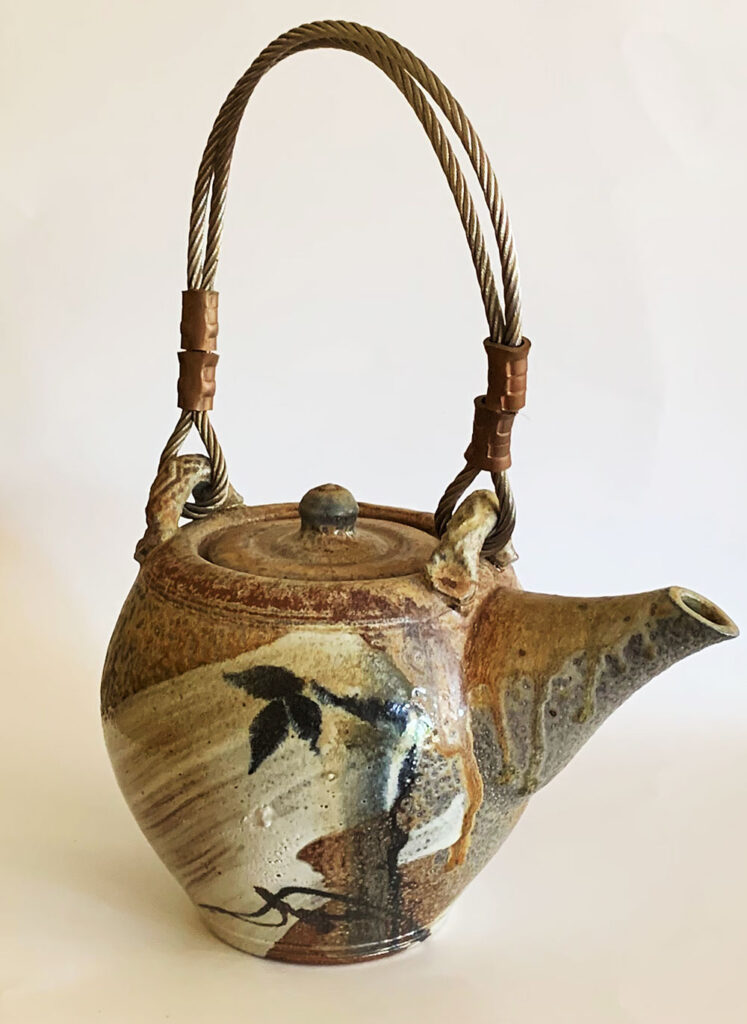
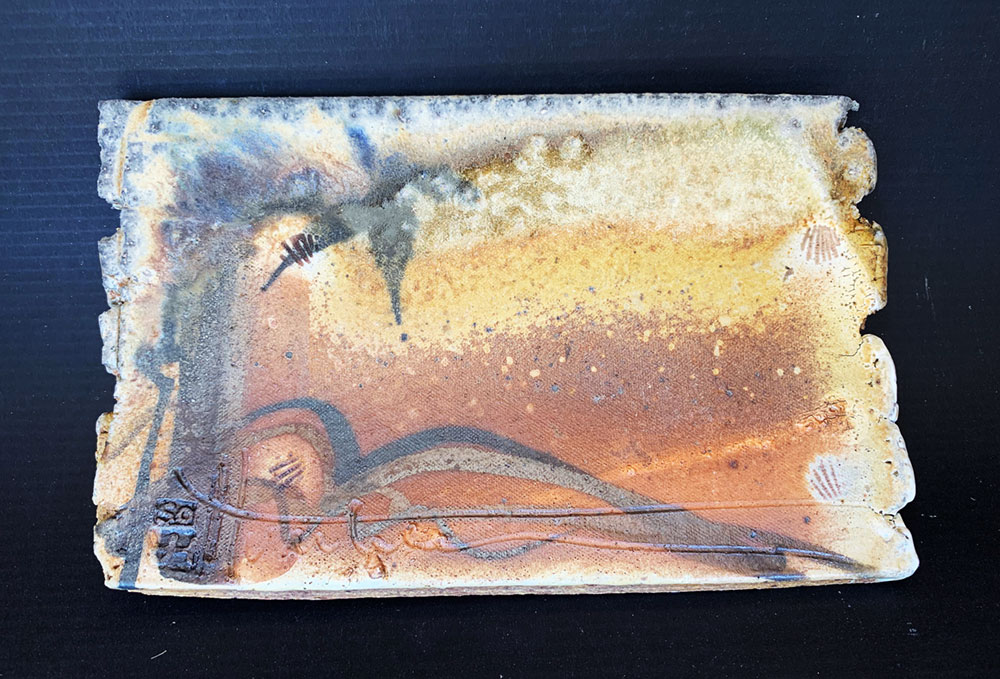
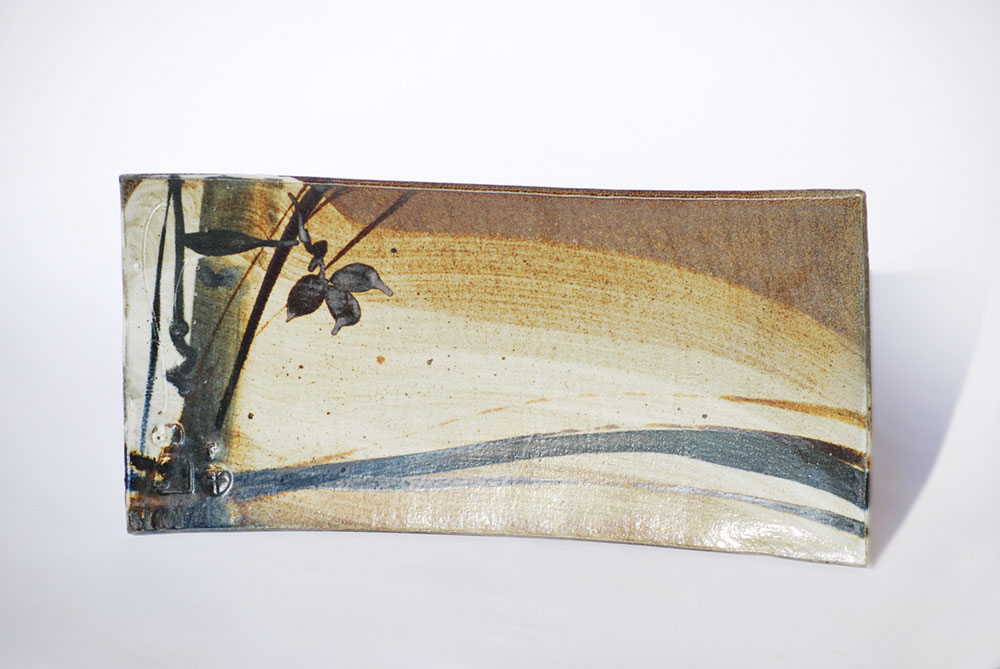
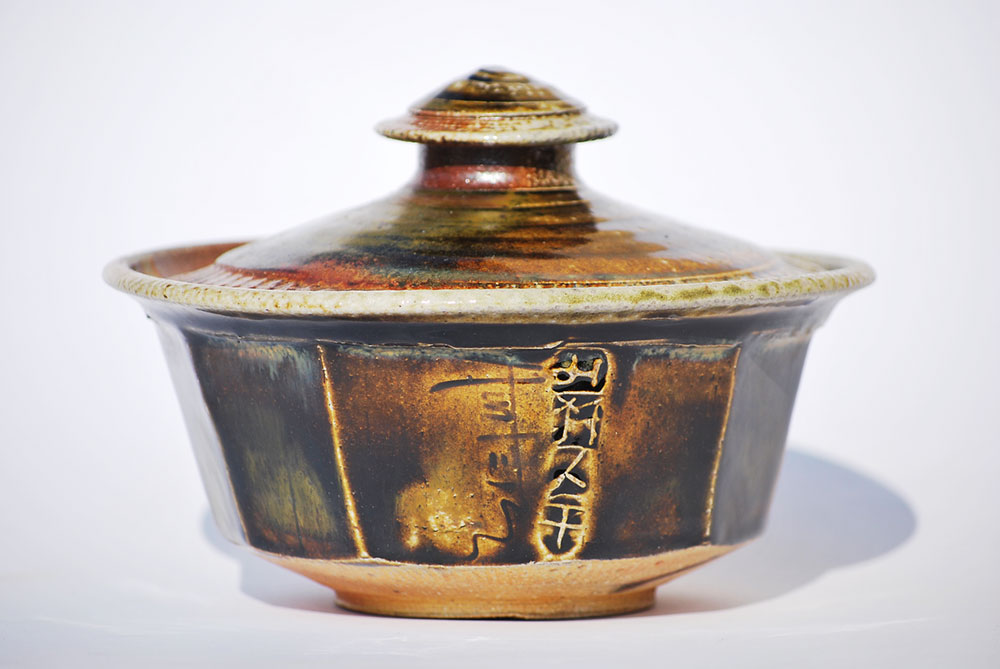
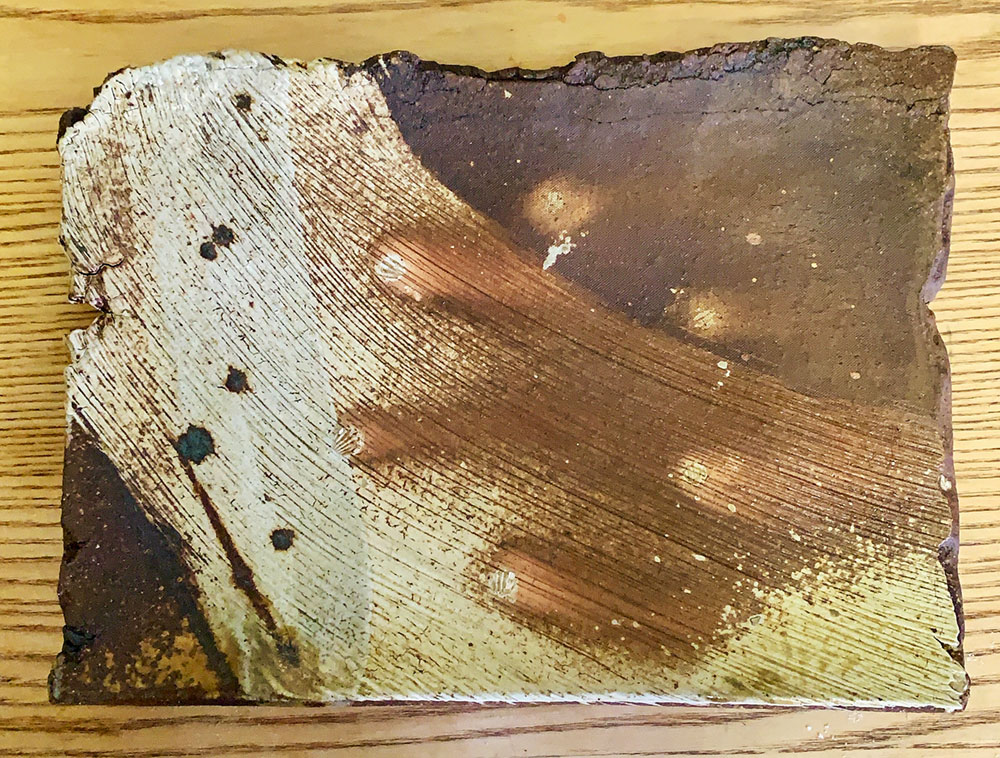
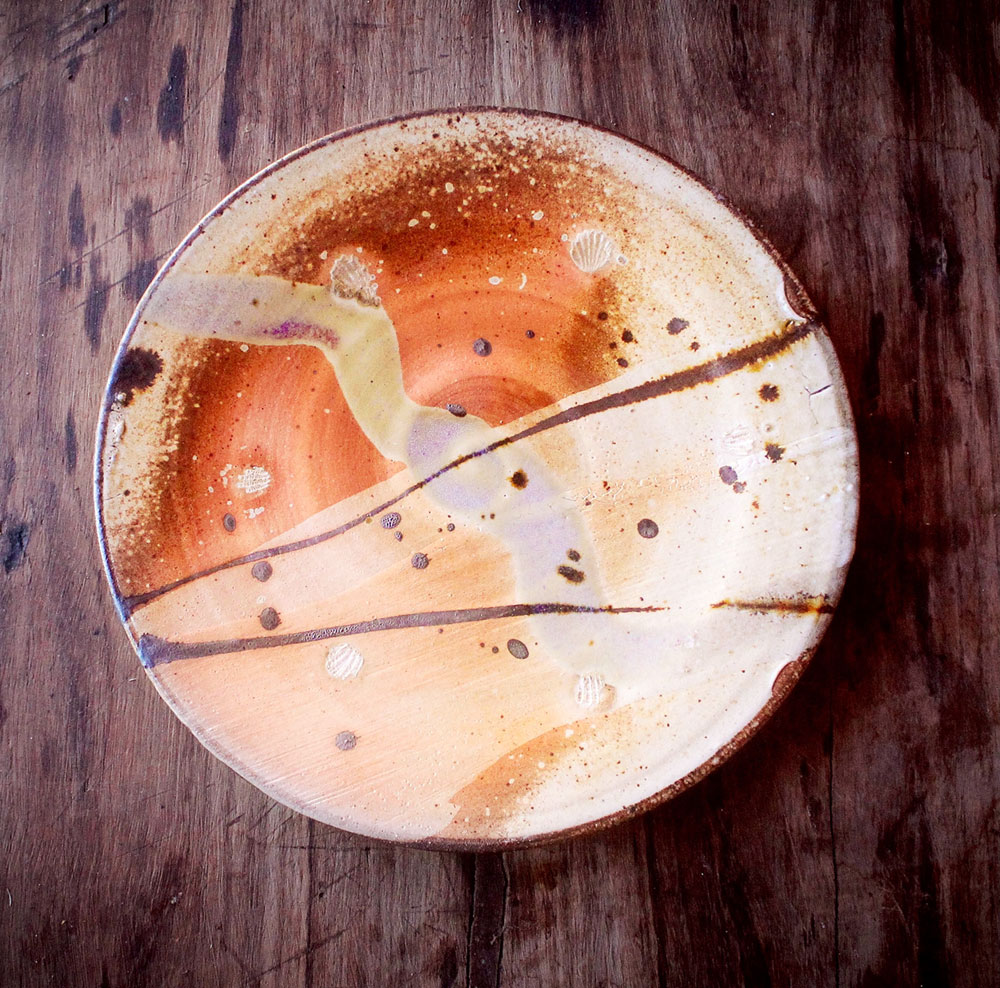
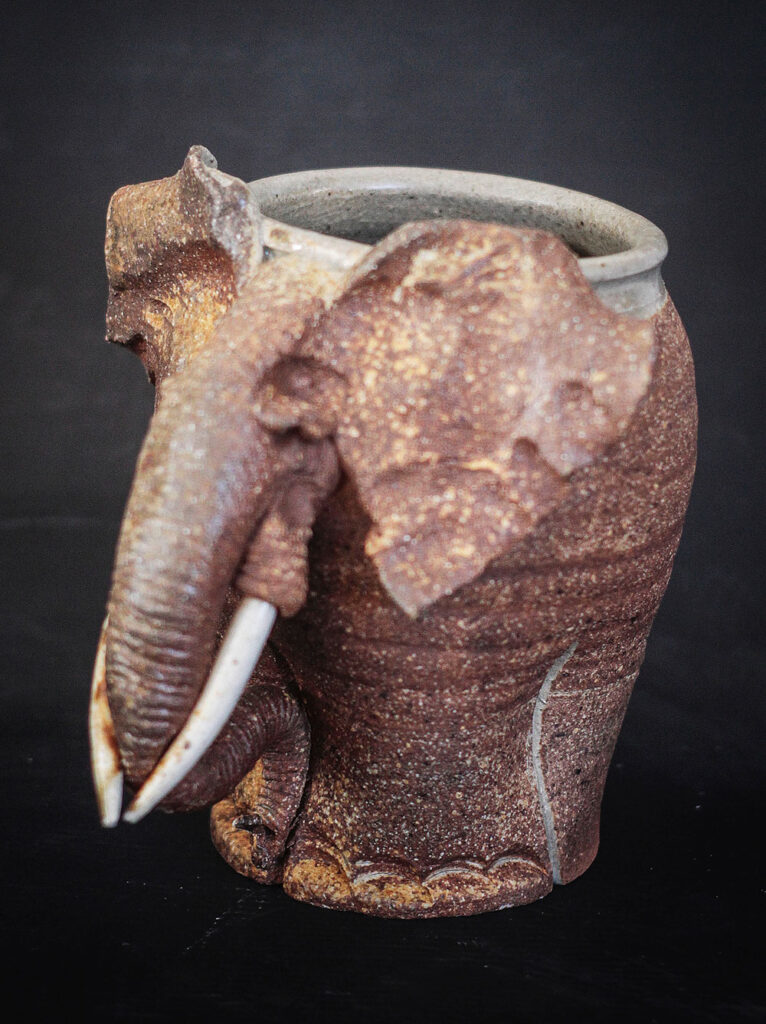
Donations can be made online at www.communityhopeministries.com
More about his life and work available at www.themasterpotter.com.
Donations may be made by EFT to:
Community Hope
Nedbank of Namibia
Windhoek South Branch
Bismarck Street PO Box 1
Windhoek, Namibia
Branch code: 461-629
Acct # 11000211216
Donations may be made on the website via PayPal.
Or sent to P.O. Box 2108, Lindale, TX 75771
Community Hope is a non profit 501(c)3 organization.
Images and text: Copyright John Hunter
Woodfiring.com thanks John Hunter for their collaboration in the preparation of this article.