My ceramics career commenced in the 1970’s-80’s which led to a then traditional training as a apprentice production potter at Sturt Workshops in Mittagong, New South Wales, Australia. Sturt was the first production ceramics workshop established in Australia by the late Ivan McMeekin. My curiosity for raw materials commenced at Sturt under the guidance of the late Ian McKay where we would make our own clay bodies for throwing. Since then I have continued exploring natural clays for making and glazes.
Being trained as a production potter the ‘old school way’ was of great benefit. A real hands on approach. Focusing in on the task at hand, getting lost in the process where pots were not being made but born.
During this time I was introduced to wood firing and salt glazing by the late Janet Mansield.
Since leaving Sturt I established my workshop on the mid north coast of New South Wales maintaining my practice as a wood firing potter.
I initially built a phoenix fast fire kiln which I used for salt glazing before relocating my workshop to its current location.
I then constructed a Bourry double firebox kiln. I was making functional tableware and salt glazing.
During 2006 I was invited to attend the International Workshop of Ceramic Art in Tokoname (IWCAT). I truly felt like I had ‘arrived home.’ During my time there I visited many ancient kiln sites including Bizen, Shigaraki, Hagi, Mino, Seto and Tamba. This left an indelible mark on my career as a potter and when I returned home I built an anagama kiln.
I have since replaced my bourry box with a catenary arch kiln. I am currently firing works in both kilns using local hardwood timber.
It takes me about a week to pack the anagama, 4 days to fire, 3 days to cool before unpacking. The works are mostly bisque fired. My glazes consist of feldspathic glazes which I like to layer, and various ash glazes. I start with a small fire slowly building up embers. The kiln is put into reduction around cone 06 (990) however by this time after every stoke there is a degree of reduction occurring.
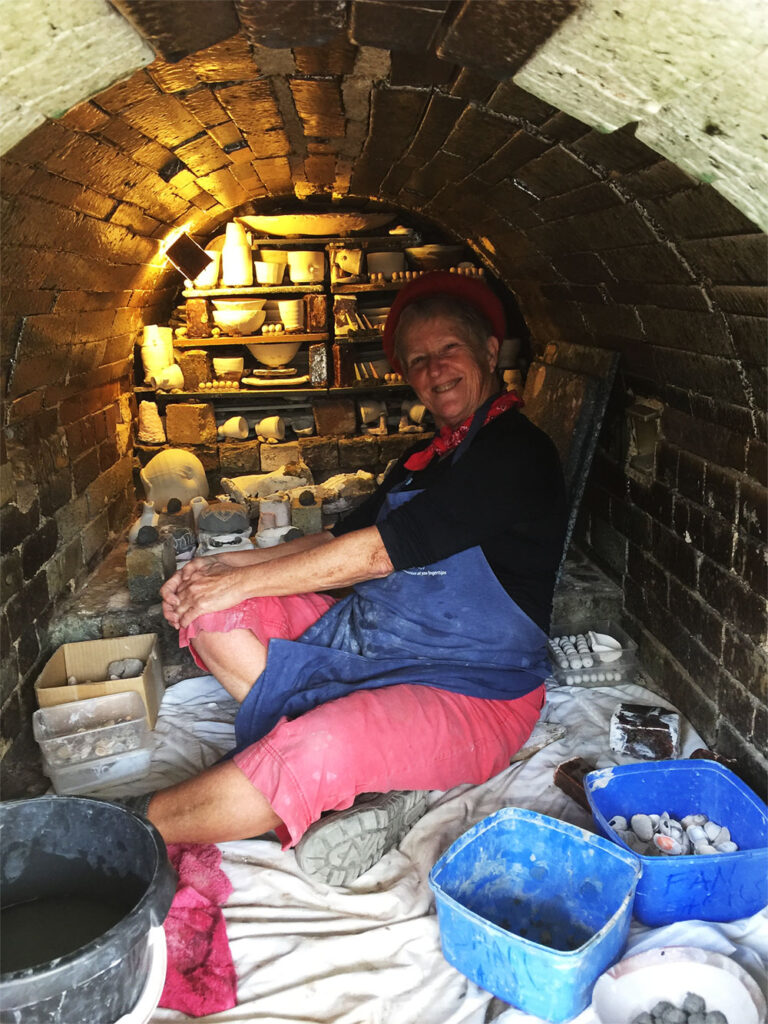
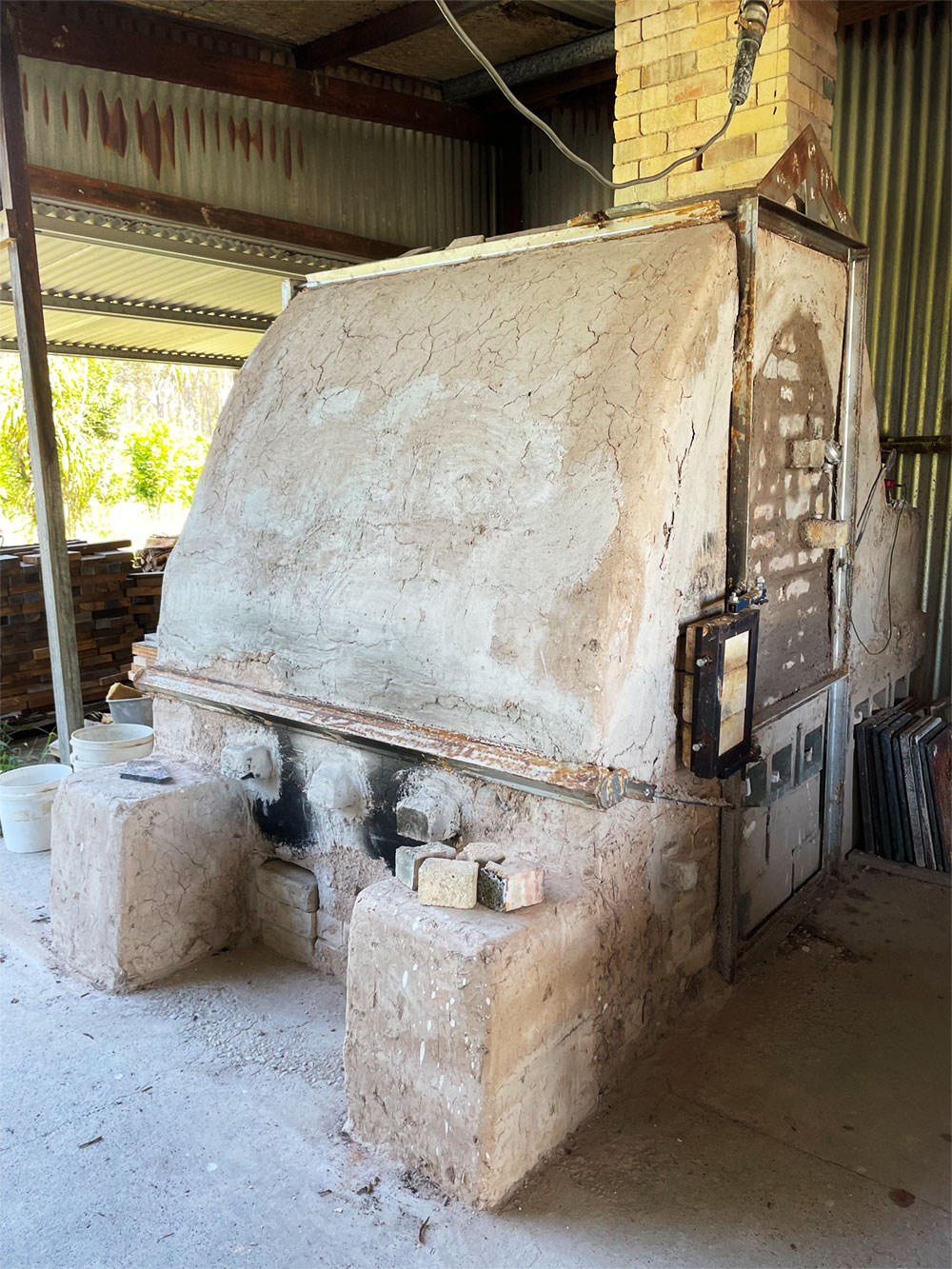
Side stoking commences when cone 8 is starting to go in the front building up embers at the back of the kiln and then letting them burn down before side stoking again. These cycles fluctuate around 4-6 hour intervals. I continue firing under reduction relying on fly ash for glazing works in the firebox until cone 11 – 12 are over. I like to reduce cool in this kiln giving a matt quality to the fired surface.
My catenary is a slightly different process where works have a liner glaze inside and partly on the outside. I fire in a similar way for 30-40 hours. I am currently exploring the introduction of soda into this kiln. This kiln is so efficient using much less wood, firing even throughout and is a dream to fire.
I returned to Japan in 2019 making and firing an anagama with John Dix at Fieldworks and visiting ancient kiln sites in the Shigaraki, Tamba area.
I make mainly on a kick wheel and use an electric wheel for larger works. I am finding that I am making more and more on my kick wheel and content to accept works that come off the wheel with a fluid spontaneity a subtle movement reflecting the nature of the material and life. Works that capture a sprezzatura essence.
While predictability of a clay body is very important for commercial production, I value the individuality that comes from using native clay. My interest in raw materials and what they will do when subjected to fire…exploring materials not for what they are but what they will do ….
My work reflects my lifestyle observing geological formations, travelling through wide open spaces, hiking mountains, my love of the ocean and zest for life…I want my pots to reflect these qualities. I want to make works that reflect an Australian landscape, have a soulful spontaneity, resonate with the user, perform their function and bring joy to the user.
It took me years to learn to make and the rest has been learning to unmake and find my own voice.
I want my works to sing and show marks by the maker.
It is a lifelong journey.
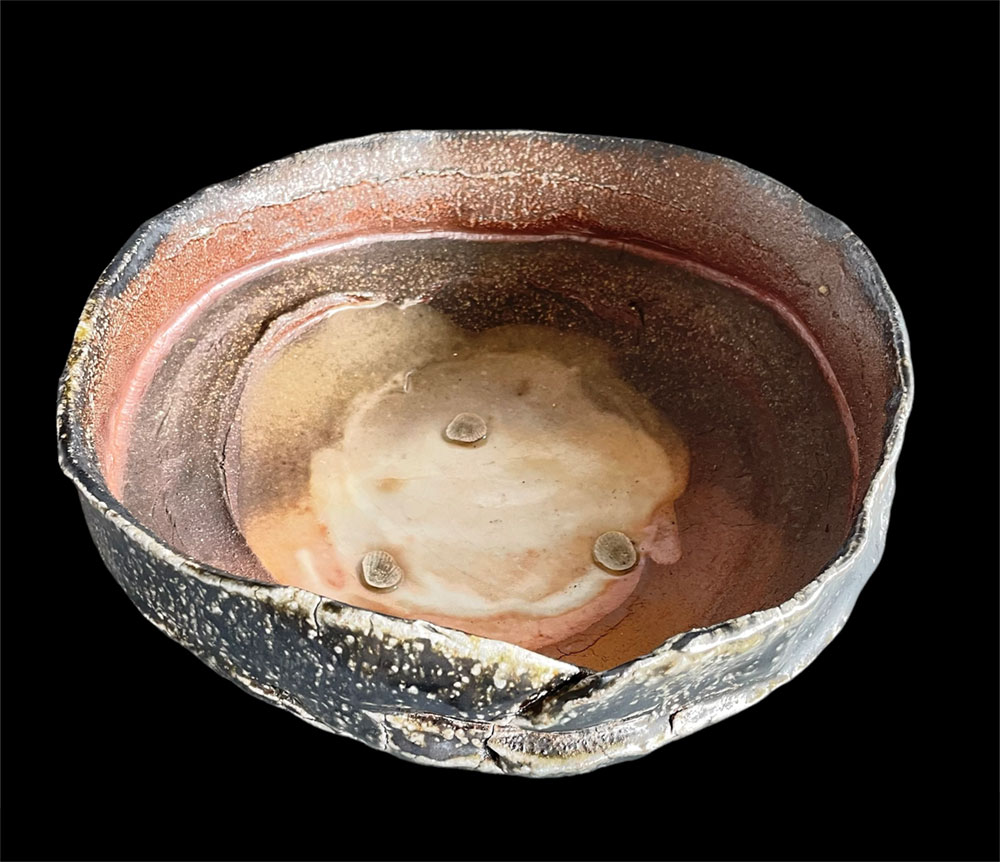
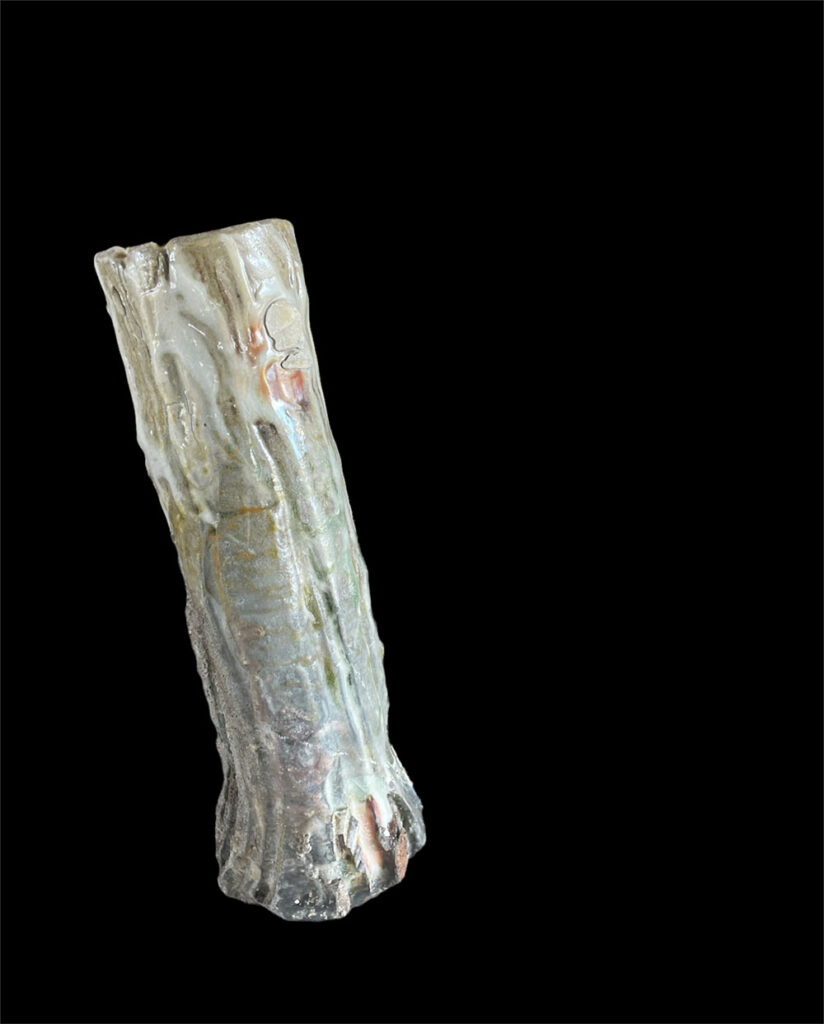
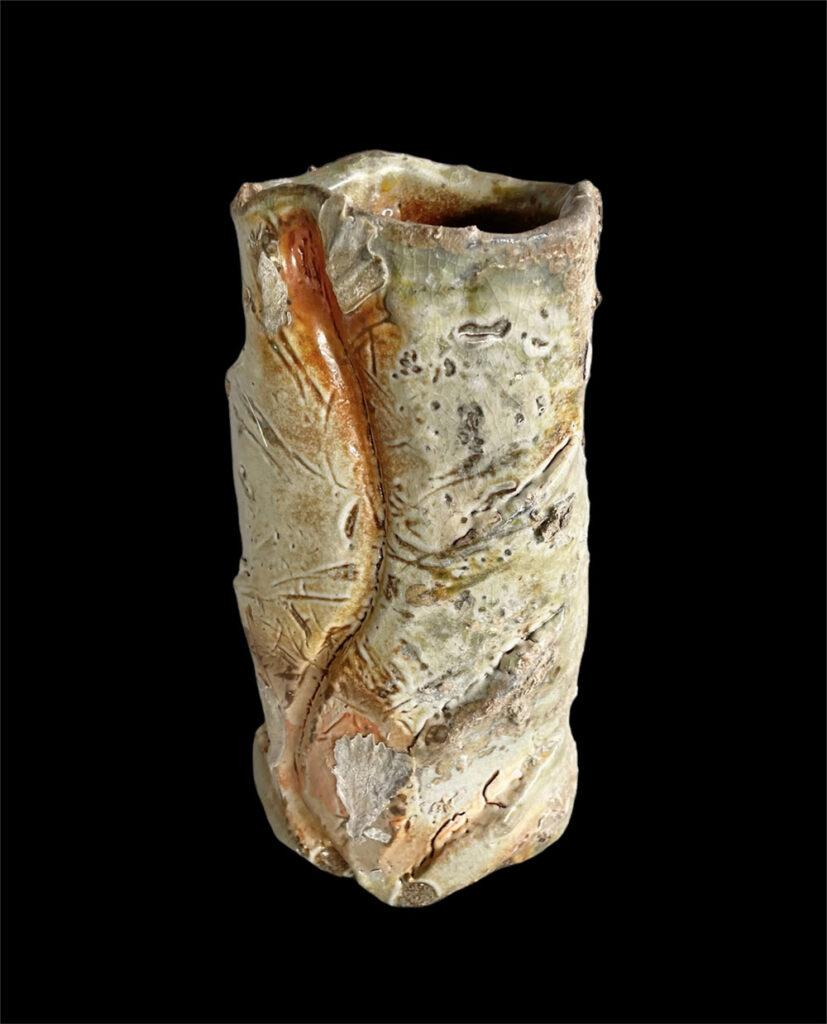
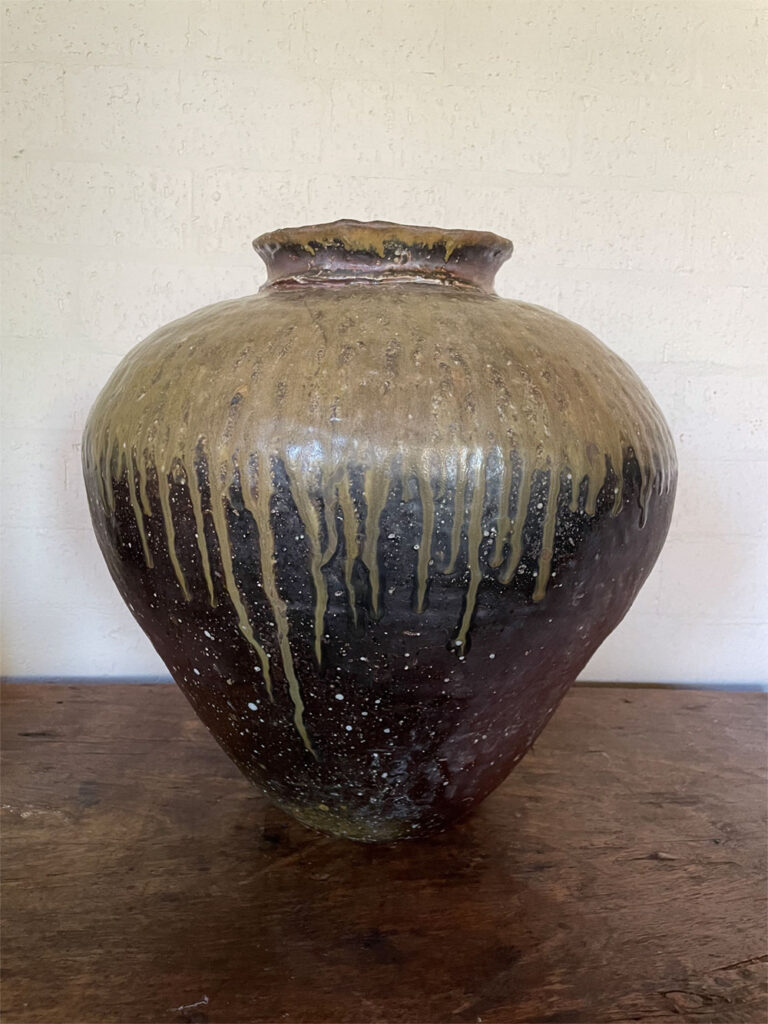
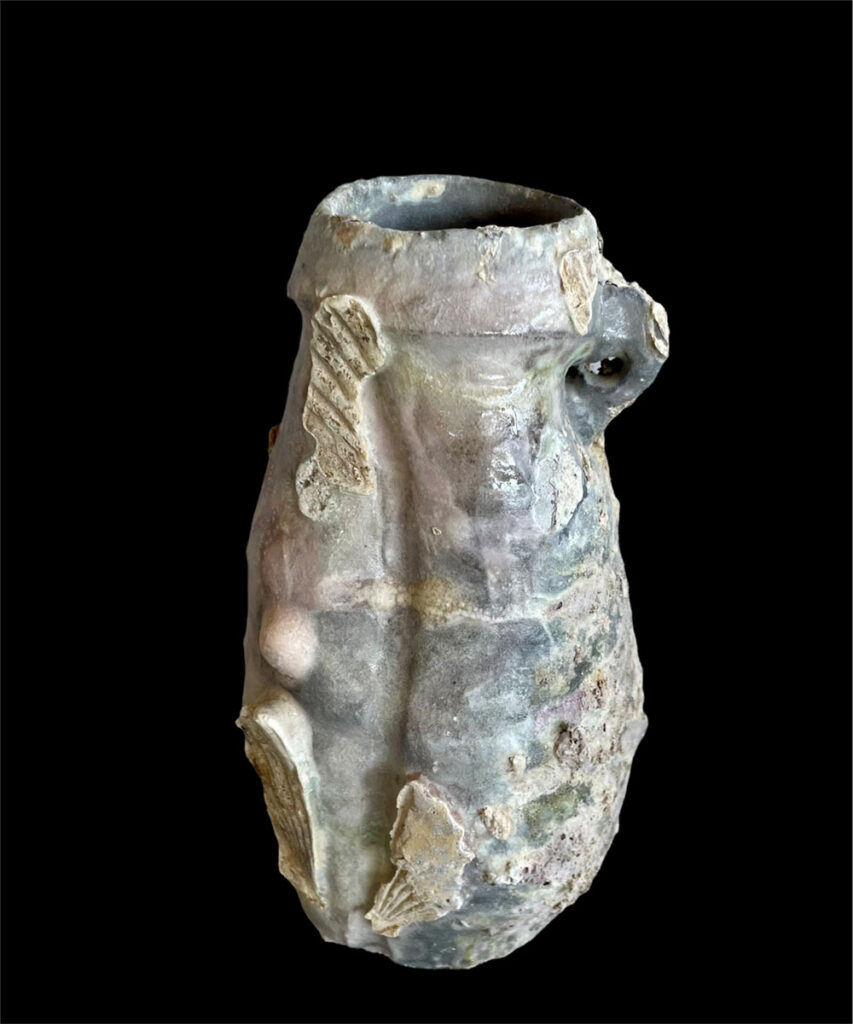
Images and text: Copyright Jann Kesby
Woodfiring.com thanks Jann Kesby for their collaboration in the preparation of this article.